Plastic is good.
there. We said it.
Plastic is good. As long as they are properly recycled.
Through the cursor internet search, about 350 million tons of plastic waste will be created every year. It is a lot of plastic. The only good thing about that figure is that there are many plastics that can be reused and recycled. In Fairphone, we always believed in reuse and recycling as much as possible as much as possible. In 2015, we first started using recycling plastics on smartphones. By 2021, we launched Fair Phone 4 with 100% consumer recycling (PCR) plastic on the back cover of the world’s first smartphone. that Fair phone 5 I developed this further. 75% of the total structural plastics used in it are made of 100% PCR plastics. It’s not just a smartphone. More than 80% of weight Fairbird XL It is made of structural plastic parts and is all 100% PCR plastic. Our new phosphorus Fairbird If 98%of the plastic used are recycled varieties after consumers, it is higher.
About 350 million tons of plastic waste is produced every year. Unfortunately, many people are lost to landfills, abandoned or incinerated in waters.
But what exactly is the recycling plastics after consumer?
Plastics can be divided into two main categories. The first is polyethylene (PE) and polypropylene (PP) varieties, we can club broadly with regular plastic. This can be seen in the surrounding world, from plastic bags and pet bottles to sticky tape and clinging films. Other categories are engineering plastics, which include thermoplastic polymers, such as nylon, ABS (or acrylonal butadiene styrene) and polycarbonate (PC). Using a smartphone (and most electronic devices, most electronic devices for that problem), in most cases, PCs (usually PCs) are used due to impact strength and structural integrity. With a pair phone, it is more important to ensure the highest quality of the original plastic source. Because we are recycled as a complex electronic device that is not simpler, such as plastic buckets or pots.
What is the recycling plastics after prior consumer to consumers? Virgin plastics are originally molded and assembled into various plastic products used in daily life by arriving at the original primitive resin type. The remaining things in this process, such as trimming or defect parts, are often regenerated and reused. This is what we call prior consumers. Or do not leave the factory before being recycled to follow the industry’s point of view, after industrialization.
In contrast, after -consumer recycling plastic comes from the already used, discarded and collected products after reaching the end of life. This is especially meaningful because plastic waste is circulated from the environment. This not only facilitates the demand for virgin plastics, but also closes the loop of material reuse, leading to a more sustainable and circular economy. By increasing the demand for PCR plastics, we encourage the creation of better collection and recycling systems. It is a fair thing to do for the earth and us.
In the case of pair phone products, the main source of PCR includes large PC water bottles and jerry cans, headlights of cars, and small disks. If you use Fairbuds XL, we used a PC in the Wafer Carrier Box that can be found extensively in the semiconductor industry. This box was eventually used several times before recycling, and it was suitable for the supply chain if high quality was given.
What about the process?
Unfortunately, many plastic waste is lost to landfills or incineration. Then there is a wrong management problem, which leads to plastic dumping in the sea, rivers and other water. The part of the recycling stream is collected by local governments or private parties from large corporations to independent waste speakers. Then the collected plastic waste was sent to the waste distributor and sent to the separator, scrap dealer and recycling resin producers. The whole process includes decomposition, crushing and cleaning. Eventually, the plastic mass is heated and melted and cut into raw plastic pellets.
Then this raw pellet adds additives to add additives to modify the characteristics of the pellet to optimize for injection molding. This modified pellet is what we use in the manufacturing process. The entire process is less than 50%to 80%of carbon -intensive compared to the virgin plastic production. It is a peripheral of raw material exploitation, and it is perfectly meaningful to make energy -intensive distillation, polymerization and granules into raw material petroleum.
What is the problem of PCR plastic work?
The manufacture of electronics, especially the plastics required for smartphones, must meet very high specifications. This limits the source plastic to pure and clean waste. It is becoming more and more important to build more supply chains for various types of plastic waste. Virgin plastics can be used to control the quality of the generated plastics very easily, but using PCR can directly affect the quality of recycling plastics if the raw materials are very dirty or greatly degraded. This is one of the reasons why it is more difficult to work with Ocean Plastic to create recycled plastics.
In addition, there is a problem of plastic waste from multiple sources and various types, making it more difficult for recyclists to classify and standardize recycled plastics. That’s why raw plastic waste disposal itself is also important. The durability and life of the final PCR pellet depends on how the complex and recycler handle the waste itself.
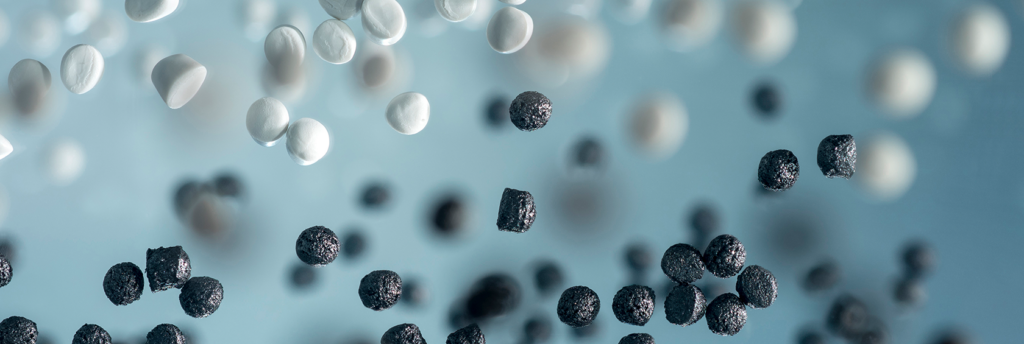
Polycarbonate granules -image rights: covestro
But over the past few years, the situation has been improved due to the leap and boundaries in the plastic recycling space. Large polymer giants, such as COVESTRO and SABIC, have achieved major development of quality control, especially in relation to PCR plastics for manufacturing smartphones. The recycling companies they work are maintained at a high level and are the main push to standardize the quality of recycling plastics, including color. Even five years ago, this big player will be much more difficult to push PCR among electronics manufacturers, considering the requirements for functions such as virgins such as accurate color matching and absolute transparency. But now, new technologies and trends, such as chemical recycling and PCR without PFAS, are no longer difficult to sell. Chemical recycling decomposes the original waste plastics into a molecular form, making the resulting PCR almost identical to the virgin plastics. And PFA? Most of the plastic fire truck additives in polycarbonate contain PFA (or per and polyfluoroAlkyl) material. But PFA materials are also called “Forever” chemicals. Because they are terrible in the environment because they are difficult to collapse. europe
Is the product made with PCR is less durable than a product made of virgin plastics?
We can’t talk about all the products, but in relation to smartphones and audio products, the product range of FAIRPHONE maintains the same strict test as other electronic manufacturers need to proceed. that Fair phone 5 The drop test of military grades disappeared at 1.6m and 1.8m, and it was not completely damaged on the other side. that Fair phone 5 It is also applied to water jets and dust tests and received an IP55 resistance rating for dust and moisture. This is especially impressive, given that there are no adhesives used in the device. Both Fairbird and Fairbird XL In addition, we were able to withstand tests and rain winds and successfully organized. It is also worth noting that all recycled plastics used in the device must remove multiple quality management tests verified by third parties. In the design stage itself, if you think that PCR plastics may not be enough in certain areas such as impact strength, you add ribs to the structural design while considering the entire weight.
In summary, we can confidently say that our products are not durable than other electronic devices that do not use recycled plastic. In fact, in combination with our modular design, long warranty and longer support Windows, it is much more durable than competitors. After all, in FAIRPHONE, it is very serious about the product design designed to persist.